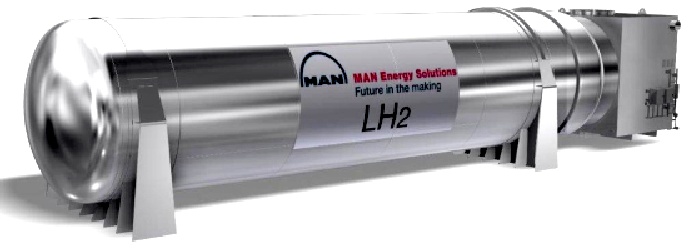
MAN Cryo, the wholly owned subsidiary of MAN Energy Solutions,
has, in close cooperation with Fjord1 and Multi Maritime in Norway -
developed a marine fuel-gas system for liquefied hydrogen.
Multi Maritime’s hydrogen vessel design for Fjord1, including the fully integrated MAN Cryo – Hydrogen Fuel Gas System, has been granted preliminary approval in principle (AIP), by the DNV-GL Classification society. The award is significant in that the system is the first marine-system design globally to secure such an approval.
The system has a scalable design that allows easy adaptation for different shipping types, sizes and conditions. The design is suited for both above- and below-deck applications, offering ship designers the flexibility to optimise their designs in relation to efficiency, and to cargo or passenger space.
Liquefied hydrogen has a temperature of -253 °C and is one of the absolutely coldest cryogenic gases there is, which places system components and materials under extreme stresses. Another design challenge was hydrogen’s explosive nature, with the MAN Cryo engineering team accordingly placing top priority on safety.
Once liquefied, hydrogen is reduced to 1/800th of its volume compared to that of its gas phase, facilitating a more-efficient distribution. As a fuel, hydrogen does not release any CO2 and can play an important role in the transition to a clean, low-carbon, energy system. Liquefied hydrogen can be used to charge batteries for electrical propulsion via fuel-cell technology.
Shipping in particular is facing great challenges with regard to more environmentally-friendly fuel sources, which is why MAN Energy Solutions has argued in favor of what it terms a ‘Maritime Energy Transition’ for some time as the most promising way to achieve a climate-neutral shipping industry.
The term ‘Maritime Energy Transition’ stems from the German expression ‘Energiewende’ and encapsulates MAN Energy Solutions’ call to action to reduce emissions and establish natural gas as the fuel of choice in global shipping. It is also an umbrella covering all MAN Energy Solutions’ activities in regard to supporting a climate-neutral shipping industry.
It
is conceivable that a suitably modified 'Elizabeth Swann' might circumnavigate
the world on one fill up (in two tanks) of liquid hydrogen, first proposed on this
website in July 2021. It is also possible, that a hydrogen and solar
powered hybrid combo, might accomplish such a voyage in under 80
days, as in Jules
Verne's famous novel: Around
the World in Eighty Days.
There
would be many challenges to such an endeavour, not least of which is
making the bunkering arrangements in a world that is only just limbering
up for the transition to zero
emission waterborne
transport. LH2 holds potential for cargo transport, provided that
filling stations at ports are established along with transfer logistics,
from manufacture, or better still, conversion on site at ports and
harbours. Again, this is one of the challenges the world is facing,
where at the moment, the fueling choices for fleet operators are far
from clear. It is an investment quagmire.
Liquid hydrogen requires cryogenic storage technology
with special thermally insulated containers, as an inner and outer
cylinder, and requires special handling common to all cryogenic fuels. This is similar to, but more severe than liquid
oxygen handling.
See purging requirements below, as another example of the challenges to
come to terms with.
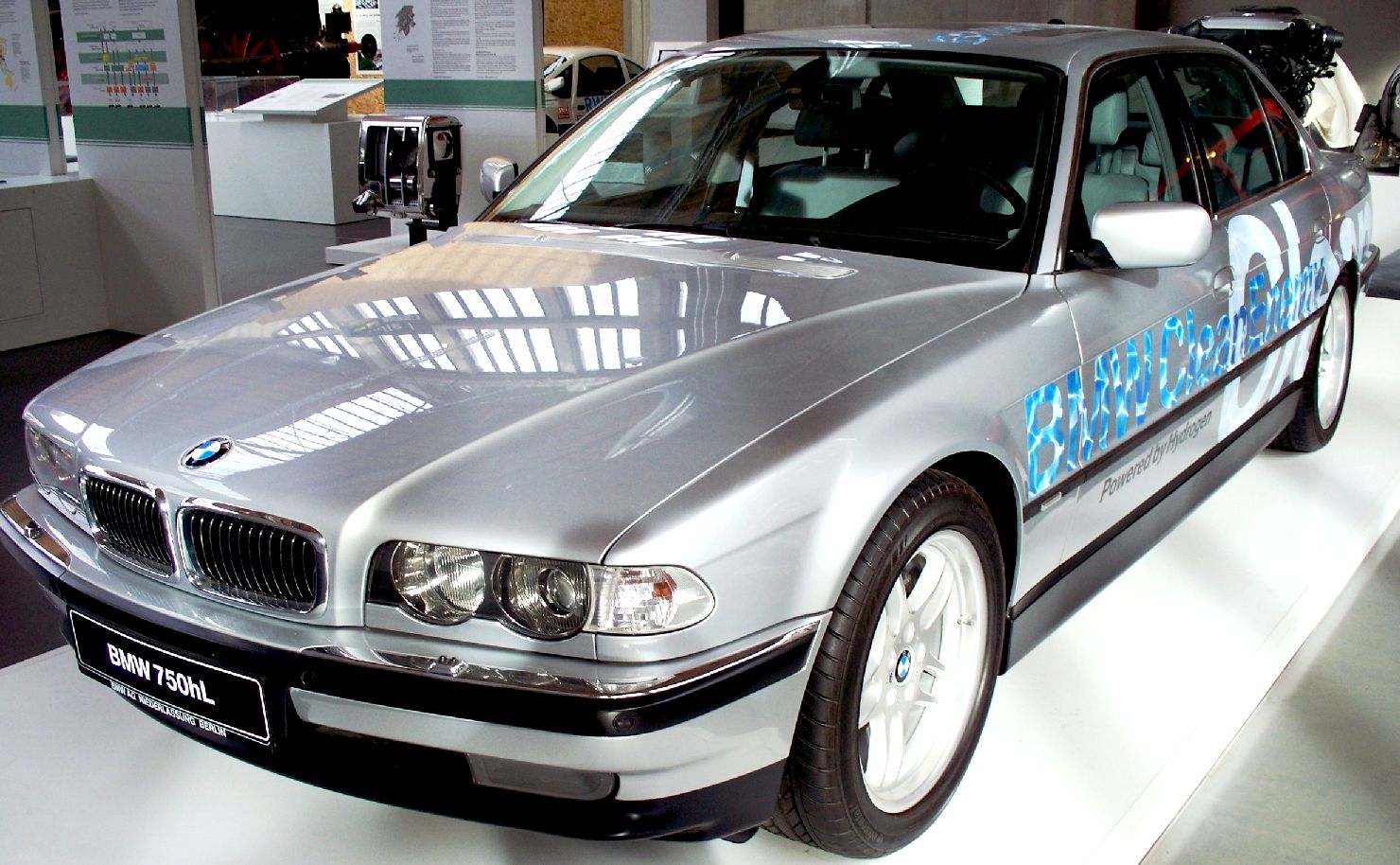
BMW
LH2 - The heart of the 750hL is a hybrid, V12-cylinder internal
combustion engine with two independent electronically controlled fuel induction systems. These systems allow the 750hL to run on either gasoline (petrol) or hydrogen.
The car was launched in 2000.
The 750hL has a hybrid 12-cylinder petrol
engine capable of running on either gasoline or hydrogen. The 5.4-liter engine has two independent, electronically controlled fuel induction systems. The hydrogen engine offers excellent torque and acceleration, while the specially insulated 140-liter tank for the liquid hydrogen provides a range of 400 kilometers.
By cooling hydrogen to -253 degrees Celsius, hydrogen is shrunk to a thousandth of its original volume. 70 layers of aluminum and fiberglass sheets between the exterior and interior vehicle walls insure that the liquid hydrogen remains at extremely low temperatures.
Naval architects are
struggling to find safe mass storage solutions for cargo and cruise ships,
hence the EU's call for proposals under their exclusive ZEWT
partnership: Zero
Emission Waterborne Transport.
Most are headed towards multiples of Type IV composite cylinders and
proportionally higher operating pressures - as the linear development
route. We can see why. It is the
obvious choice if trying not to alter existing hull designs. Why change
if you don't have to. Modern ship hulls are a very efficient way of
moving goods around the world.
The investment in a new ship is
staggering, written off over some 15-21 years. Hence, you cannot blame fleet operators
only investing in proven technology. We owe merchant navies a big vote
of thanks, for giving us the means to trade internationally, so
enriching our lives. Equally, the scientific community should
reciprocate, by giving investors viable choices in replacing their diesel
bunkered behemoths.
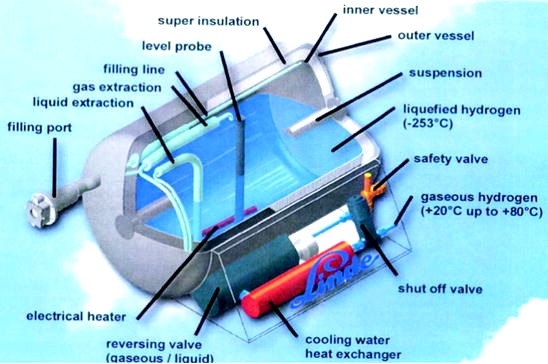
In the absence of a hydrogen pipeline supply network, which would be costly and take considerable time to build, hydrogen could be supplied using road tankers. However, transporting hydrogen by road as a compressed gas is very inefficient and supplying liquefied hydrogen (LH2) by road tanker is seen as the most effective way forward in the medium term. This will require large quantities of LH2 to be produced, stored and transported for
re-fuelling vehicles.
Liquid
hydrogen offers twice the energy carrying capacity per litre, but
wastes a lot of energy to produce. The best way of transporting hydrogen in terms of energy density is liquid hydrogen, achieving more than 2.3
kWh/litre. Hence, the containment tanks for 2,700kg of hydrogen, might
just be possible. Save for the boil off issue.
The drawback of hydrogen liquefaction is the amount of energy involved. This is partly due to the very low temperatures required to condense into its liquid state (about -253°C).
State of the art hydrogen liquefaction technology has a power consumption of 12 kWh/kg. This is equivalent to 36% of the useable energy contained in 1 kg of hydrogen (33.33 kWh/kg, see
below). This may not be the most efficient use of energy, but because of
the vast generating capacity of offshore wind turbines, it is
sustainable.
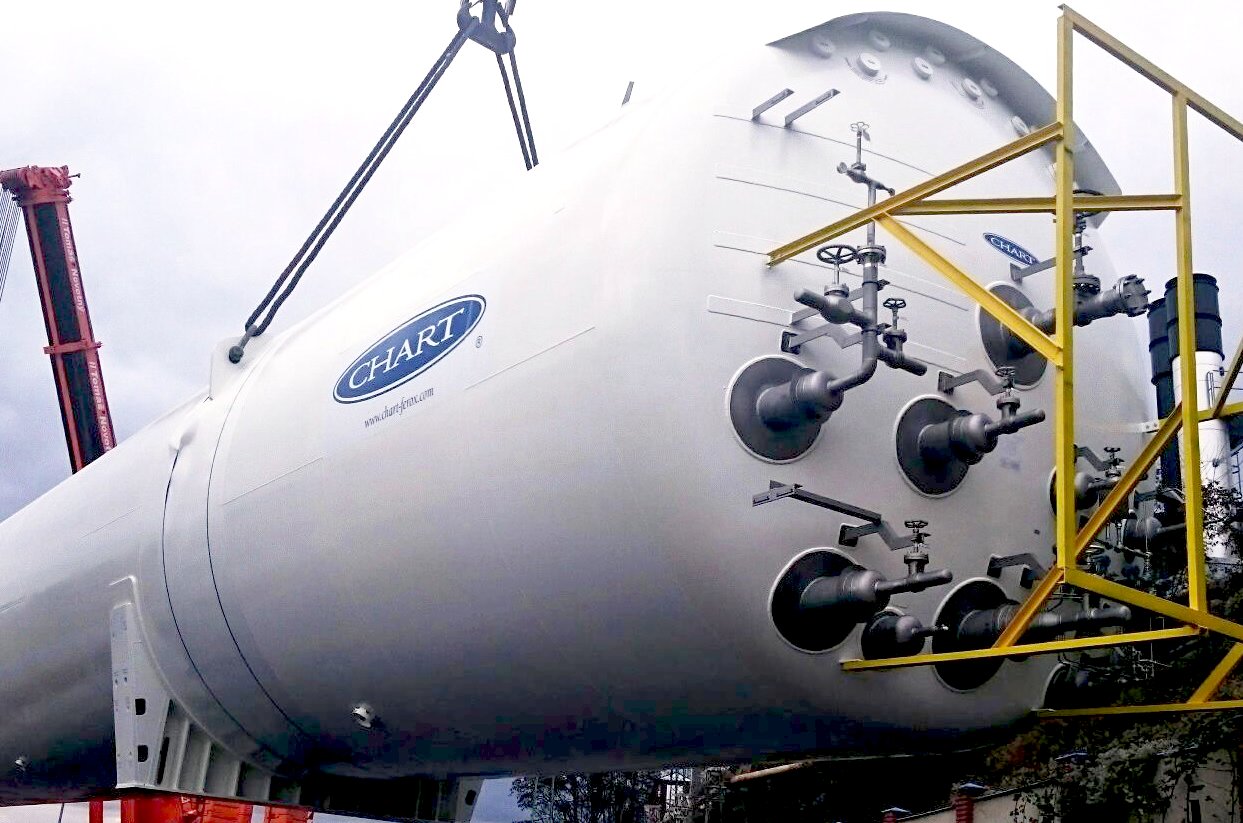
February 11 2021 -
Ballard Power Systems signed a Memorandum of Understanding (MoU) with Chart Industries for the joint development of integrated system solutions, including a fuel cell engine with onboard liquid hydrogen storage and vaporization for the transportation industry.
Both companies have provided hydrogen solutions and equipment to industry for multiple decades. This collaboration is to enable accelerated adoption of hydrogen in heavy-duty transport applications requiring long range, rapid refueling and lowest total cost, including marine vessels, buses, trucks and rail.
Liquid hydrogen is well-suited for the transportation industry as its higher density, lower pressure, and ease of filling via liquid hydrogen pump contribute to the ability for larger mobile equipment to travel longer distances similar to what is possible today with diesel fuel. As part of the development agreement:
Chart agreed to provide liquid hydrogen expertise from liquefaction plant to storage, fuelling and onboard tanks; extensive truck LNG tank experience; an existing liquid hydrogen onboard vehicle tank prototype design; fuel to vehicle connection/interface experience; LH2 test lab in Minnesota, US.
Ballard will provide Proton exchange membrane (PEM) fuel cell technology expertise; PEM fuel cell stacks, modules, and systems; fuel cell mobility experience with over 70m km of vehicle operation; market access to System Integrators and vehicle OEMs; fuel cell testing facilities in British Columbia, Canada, and Denmark.
Liquid hydrogen can be used as the fuel for an
internal combustion engine or
fuel cell. Various submarines (Type 212
submarine, Type 214 submarine) and concept
hydrogen vehicles have been built using this form of hydrogen (see DeepC, BMW H2R). Due to its similarity, builders can sometimes modify and share equipment with systems designed for
liquefied natural gas (LNG). However, because of the lower volumetric energy, the hydrogen volumes needed for combustion are large. Unless direct injection is used, a severe gas-displacement effect also hampers maximum breathing and increases pumping losses.
Liquid hydrogen is a common liquid rocket fuel for rocketry applications — both
NASA and the United States Air Force operate a large number of liquid hydrogen tanks with an individual capacity up to 3.8 million liters (1 million U.S. gallons).
Currently, storing hydrogen in the liquid form is being reserved for certain special applications, in high-tech areas such as space travel. For example, the tanks on the Ariane launcher, designed and manufactured by Air Liquide, contain the 28 tons of liquid hydrogen that will provide fuel to the central engine. These tanks are a genuine example of technological prowess: they weigh only 5.5 tons empty and their casing is not more than 1.3 mm thick.
SOME
USEFUL LH2 INFORMATION
One liter of
hydrogen gas weighs only 90 mg under normal atmospheric pressure. It is 11 times lighter than the air we breathe.
1kg
of hydrogen = 33.6kWh of energy (approx).
Under ambient conditions, a cubic metre of hydrogen provides some 3 kWh, equivalent to 0.003 kWh per litre. Pressurised hydrogen contains about 0.5 kWh/litre at 200 bar, 1.1 kWh/litre at 500 bar and 1.4 kWh/litre at 700 bar.
1 liter of liquid hydrogen weighs: 0.15604 lbs or 0.07078 kg.
Liquid hydrogen provides 2.36 kilowatt-hours per litre.
To exist as a liquid, H2 must be cooled below its critical point of 33 K. However, for it to be in a fully liquid state at atmospheric pressure, H2 needs to be cooled to 20.28 K (−252.87 °C; −423.17 °F).
In order to maintain liquid hydrogen at this temperature, tanks must be
as near perfectly insulated as possible.
At -252.87°C and 1.013 bar, liquid hydrogen has a density of close to 71 kg/m3. At this pressure, 5 kg of hydrogen can be stored in a 75-liter tank.
Petrol at room temperature is roughly 10 times denser, so by volume liquid hydrogen actually has only about one-quarter of the energy density of petrol.
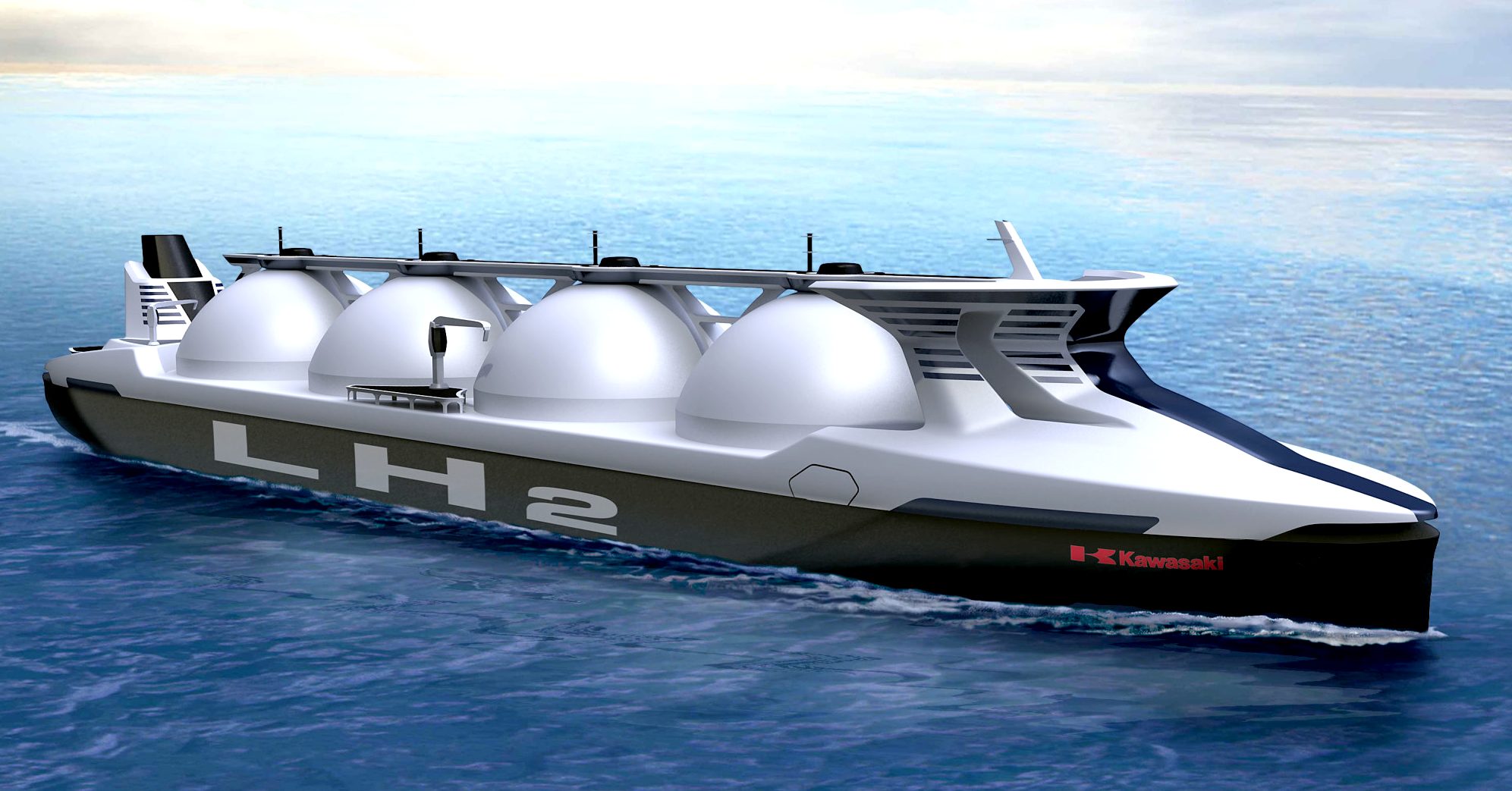
NORWEGIAN SCITECH NEWS APRIL 2015 - Wind power and CCS projects
- The Land of the Rising Sun is thinking of importing Norwegian wind and gas by sea in the form of liquid hydrogen. This could offer Norway new prospects for wealth creation and exports, say a pair of Norwegian researchers. (David Berstad is a Research Scientist at SINTEF Energy Research &
Petter Nekså is a Chief Scientist at SINTEF Energy Research)
On behalf of KHI, and with additional financing by Norway’s state-funded CLIMIT programme, SINTEF has started to survey the possibilities at home. KHI envisages annual shipments of around 225,000 tonnes of hydrogen, which would be sufficient to power three million cars. For Norway to generate all of this by electrolysis would require some 14 TWh of energy a year, equivalent to 10 – 12 per cent of the country’s electricity production, and it would need a significant increase in our generating and distribution capacity.
In the green certificate market, Norway is expected to produce 13 TWh of new, renewable energy annually by 2020, according to the aims of the scheme. If all of this were to be sent to hydrogen generation, the Japanese requirements as outlined above could theoretically be met via electrolysis alone. However, the necessary facilities are being developed extremely slowly, and it is not clear how rapidly production capacity will increase.
Due largely to the use of liquid hydrogen fuel for space rockets, good low-mass liquid hydrogen tanks have been developed. However, they will still be heavier and bulkier than petrol tanks, and for the same energy yield the hydrogen volume must be more than four times greater.
Liquid hydrogen is non-corrosive. Special materials of construction are not required. However, because of its extremely cold temperature, equipment must be designed and manufactured of material that is suitable for extremely low temperature operation. Vessels and piping must be selected and designed to withstand the pressure and temperatures involved and comply with applicable codes and regulations.
Tanks are usually cylindrical in shape and placed in a horizontal position. However, some vertical cylindrical tanks and spherical tanks are in use. Standard tank sizes range from 1,500 gallons to 25,000 gallons. Tanks are
vacuum-insulated. Pressure relief valves protect the tanks and are designed to ASME specifications.
SHIPMENT
Liquid hydrogen is transported by liquid
semi-trailers with a capacity of 12,000 to 17,000 gallons. The stationary tanks are filled from these tankers. Tankers are basically of the same
design as the stationary tanks but in addition must meet the requirements of the Department of Transportation.
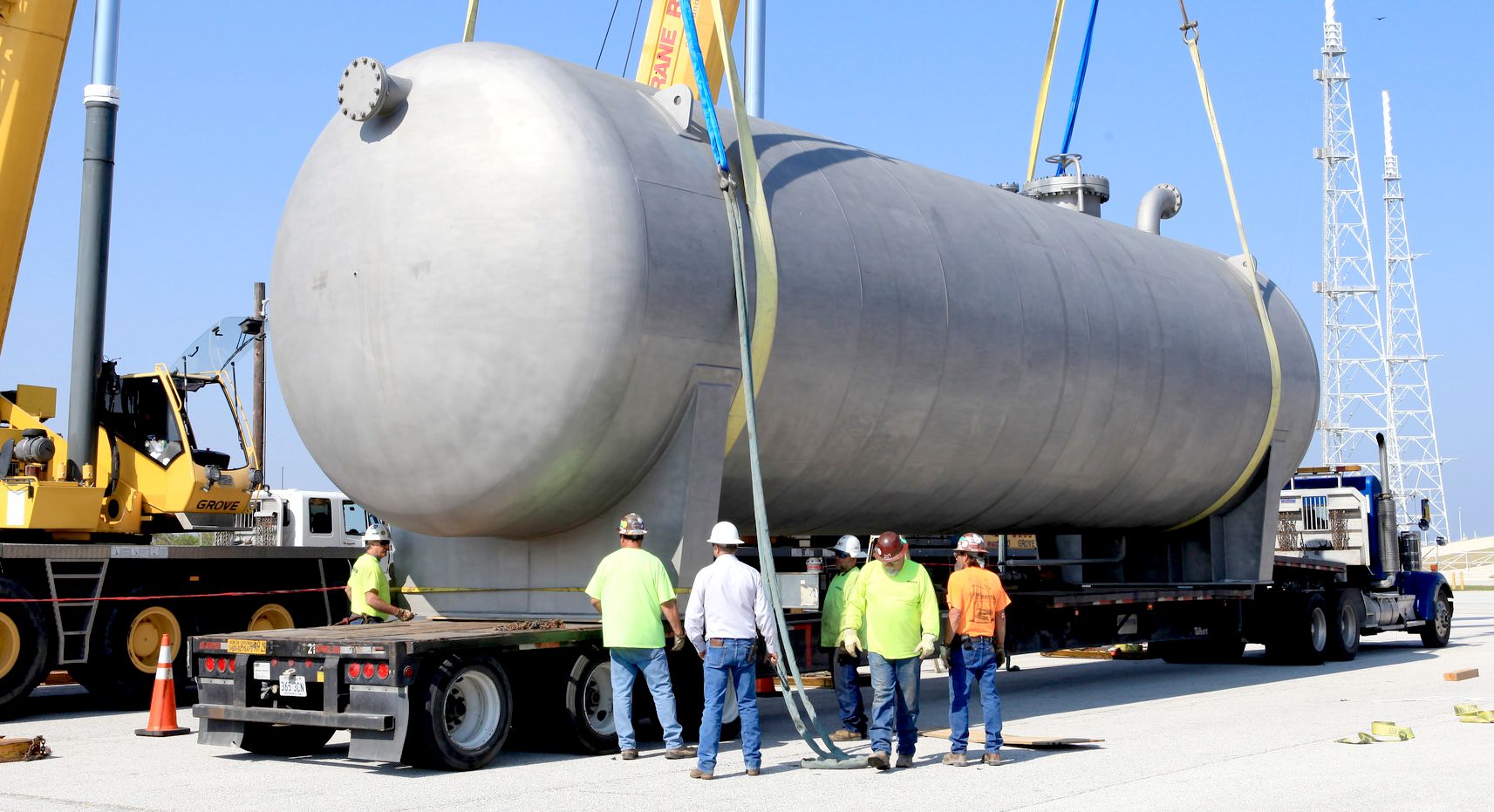
KENNEDY SPACE CENTER 1 DECEMBER 2016:
NEW LIQUID HYDROGEN TANK FOR LAUNCH PAD 39B - A new liquid hydrogen (LH2) liquid separator tank has arrived at NASA’s Kennedy Space Center in Florida. It will be used to support the agency’s Space Launch System rocket and all future launches from Launch Pad 39B.
The existing hydrogen vent system that terminates at a flare stack was designed for gaseous hydrogen. New requirements for Exploration Mission 1 and future launches include the need to address liquid hydrogen in the vent system. The new LH2 separator/storage tank will be added to the existing hydrogen vent system to assure gaseous hydrogen is delivered downstream to the flare stack.
At Pad B, the existing hydrogen vent line and supporting systems will be modified to accommodate the new LH2 liquid separator tank. The Ground Systems Development and Operations Program and the Engineering Directorate at Kennedy are performing the upgrades to Launch Pad 39B to support the agency’s premier multi-user spaceport.
The 60,000 gallon tank was built by INOXCVA, in Baytown, Texas, a subcontractor to Precision Mechanical Inc. in Cocoa, Florida. It is about 56 feet long, with a 14-foot diameter.
PURGING OF
HYDROGEN TANKS
Gaseous and liquid hydrogen systems must be purged of air, oxygen, or other oxidizers prior to admitting hydrogen to the systems, and purged of hydrogen before opening the system to the atmosphere. Purging should be done to prevent the formation of flammable mixtures and can be accomplished in several ways.
Piping systems and vessels intended for gaseous hydrogen service should be inerted by suitable purging or
evacuation procedures. If the piping systems are extensive or complicated, successive evacuations broken first by an inert gas and finally with hydrogen are most reliable. Evacuating and purging of equipment in gaseous hydrogen service should include the following considerations:
1. Evacuate the equipment and break vacuum with an inert gas, such as nitrogen. If equipment design does not permit evacuation, then pressurize and purge the system with an inert gas.
2. Repeat step 1 at least three times. If analytical equipment is available, purge system until oxygen content of residual gas is either less than or meets the process specification impurity level.
3. Hydrogen may now be introduced to the equipment.
4. Flush system with hydrogen until required purity is reached. Vent all waste hydrogen through a flue or flare stack. Any purge method should be repeated as often as required to be certain a
flammable mixture cannot be formed upon introducing hydrogen or air to the system.
|