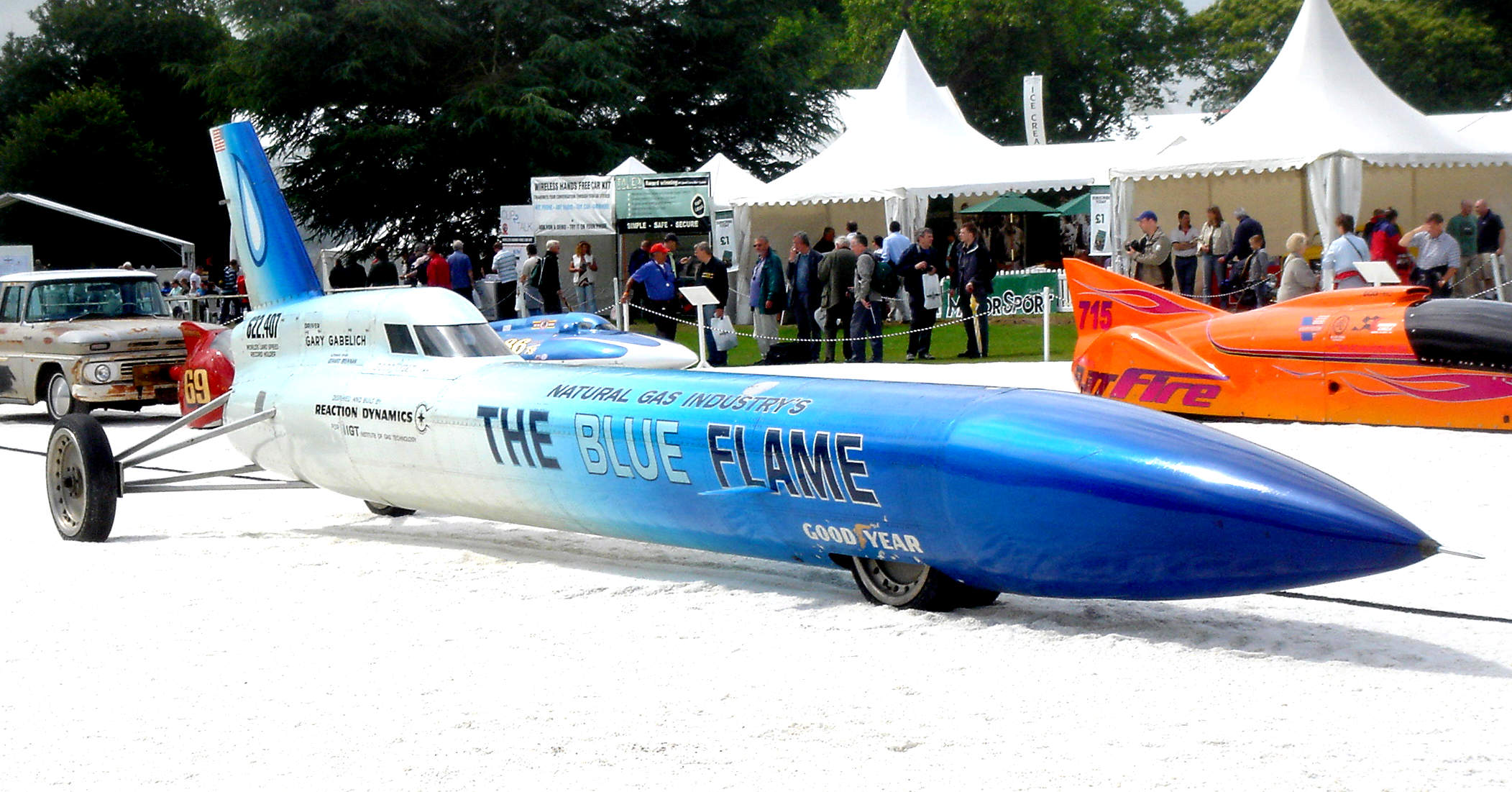
GOODWOOD
2007 - The Blue Flame, a hydrogen peroxide and natural gas powered
land speed record car driven by Gary Gabelich. The car achieved the world land speed record on Bonneville Salt Flats in Utah on October 23, 1970. The vehicle set the FIA world record for the flying mile at 622.407 mph (1,001.667 km/h) and the flying kilometer at 630.388 mph.
Blue Flame was constructed in Milwaukee, Wisconsin by Reaction Dynamics, a company formed by Pete Farnsworth, Ray Dausman and Dick Keller, who had developed the first hydrogen peroxide rocket dragster, called the X-1 and driven by Chuck Suba. The car used a combination of high-test peroxide and liquified natural gas (LNG), pressurized by helium gas. The effort was sponsored by the American Gas Association, with technical assistance from the Institute of Gas Technology of Des Plaines, IL.
The engine was designed by Reaction Dynamics and some of the components were manufactured by Galaxy Manufacturing of Tonawanda, New
York.
Blue Flame's engine is a regeneratively cooled variable thrust liquid-propellent engine. It can operate on either a single- or dual-propellant basis. In operation, it permits natural gas use as a liquid, gas, or both with a two-stage combustion start. The oxidizer flow is established first, then LNG enters a heat exchanger where it vaporizes and is brought to combustion temperature. The gas is then injected into the combustion chamber with the oxygen provided by the hydrogen peroxide. A stable flame front is established and the remaining
liquefied natural gas (LNG) is injected to bring the engine to full power.
Nominal engine running time was 20 seconds at full thrust of 22,500 lbf (100 kN), the equivalent of 58,000 hp (43 MW). Keller
stated the Goodyear Tire Company restricted their top speed to 700 mph (1,100
km/h). Reaction Dynamics subsequently modified the LNG flow in the two-stage injector system to almost halve the maximum thrust. The actual thrust during the record runs was between 13,000 lbf (58 kN) [equivalent of 35,000 hp (26 MW)] and 15,000 lbf (67 kN). Blue Flame's record runs involved accelerating continuously to the mile midpoint, then coasting through the mile. The peak speed, approximately 650 mph (1,050 km/h), was reached at that point and then the vehicle decelerated the rest of the way. The kilometer speed trap was biased towards one end of the mile, resulting in the 8 mph (12.9 km/h) higher speed.
Blue Flame uses an aluminum semi-monocoque with welded tubular structure in the nose section and an aluminum "skin." The vehicle is 37 ft 4.6 in (11.394 m) long, 8 ft 1.5 in (2.477 m) high to the top of the tail fin, and 7 ft 8 in (2.34 m) wide, with a wheelbase of 306 in (7.8 m). It has an empty weight of 4,000 lb (1,800 kg) and is approximately 6,600 lb (3,000 kg) fully fueled and loaded. Goodyear Tire and Rubber Co. designed 8:00-25 tires for the vehicle, with an outside diameter of 34.8 in (880 mm) and smooth tread surface to help prevent heat buildup, filled with nitrogen gas at 350 psi (24 bar).
Blue Flame is now on permanent exhibition at the Auto and Technik Museum Sinsheim in Germany.
When hydrogen peroxide is used as a fuel, energy is released in the form of heat during the rapid decomposition of H2O2 to H2O, creating steam and oxygen. In the case of high concentration H2O2, much of the energy takes the form of an enormous thrust - propulsion - as demonstrated
in the rocket powered cars: The Blue Flame, and the Budweiser Rocket
Car. With the Bloodhound, also considering running a peroxide rocket.
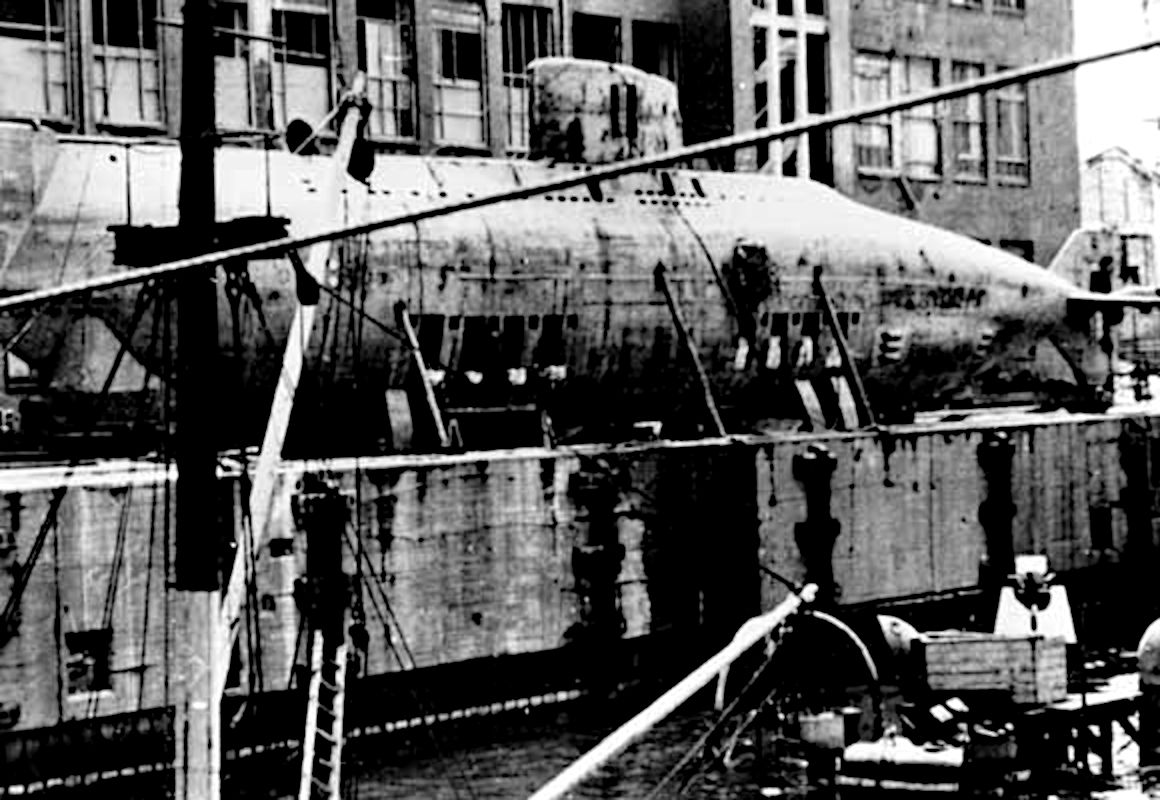
PROFESSOR
HELLMUTH WALTER
During World
War Two, hydrogen peroxide was used in German submarines (U-Boats), The Type XVII
U-boats were small coastal submarines that used a high-test peroxide propulsion system, which offered a combination of air-independent propulsion and high submerged speeds.
In the early 1930s Professor Hellmuth Walter had designed a small, high-speed submarine with a streamlined form propelled by high-test peroxide (HTP).
In October 1934 he made a proposal to OKM (Kriegsmarine high command),
suggesting build of a U-boat of some 300 tons (size similar to IIA) with
a surface speed of 26 knots and underwater speed approaching 30 knots.
His ideas were rejected promptly by the Kriegsmarine as too unconventional and fanciful.
But Walter did not give up, like his British counterpart; Barnes
Wallace.
In 1937 he showed his revised plans to Kapitän zur Karl Dönitz,
who channeled the idea more upstream.
In 1939 he was awarded a contract to build an experimental vessel, the 80 ton V-80, which achieved an underwater speed of 28.1 knots (52.0 km/h; 32.3 mph) during trials in 1940. In November 1940 Admirals Erich Raeder and Werner Fuchs (head of the Kriegsmarine's Construction Office) witnessed a demonstration of the V-80; Raeder was impressed, but Fuchs was slow to approve further tests.
Walter again contacted Karl Dönitz in January 1942, who embraced the
concept and requested that these submarines be developed as quickly as possible. An initial order was placed in summer 1942 for four Type XVIIA development submarines.
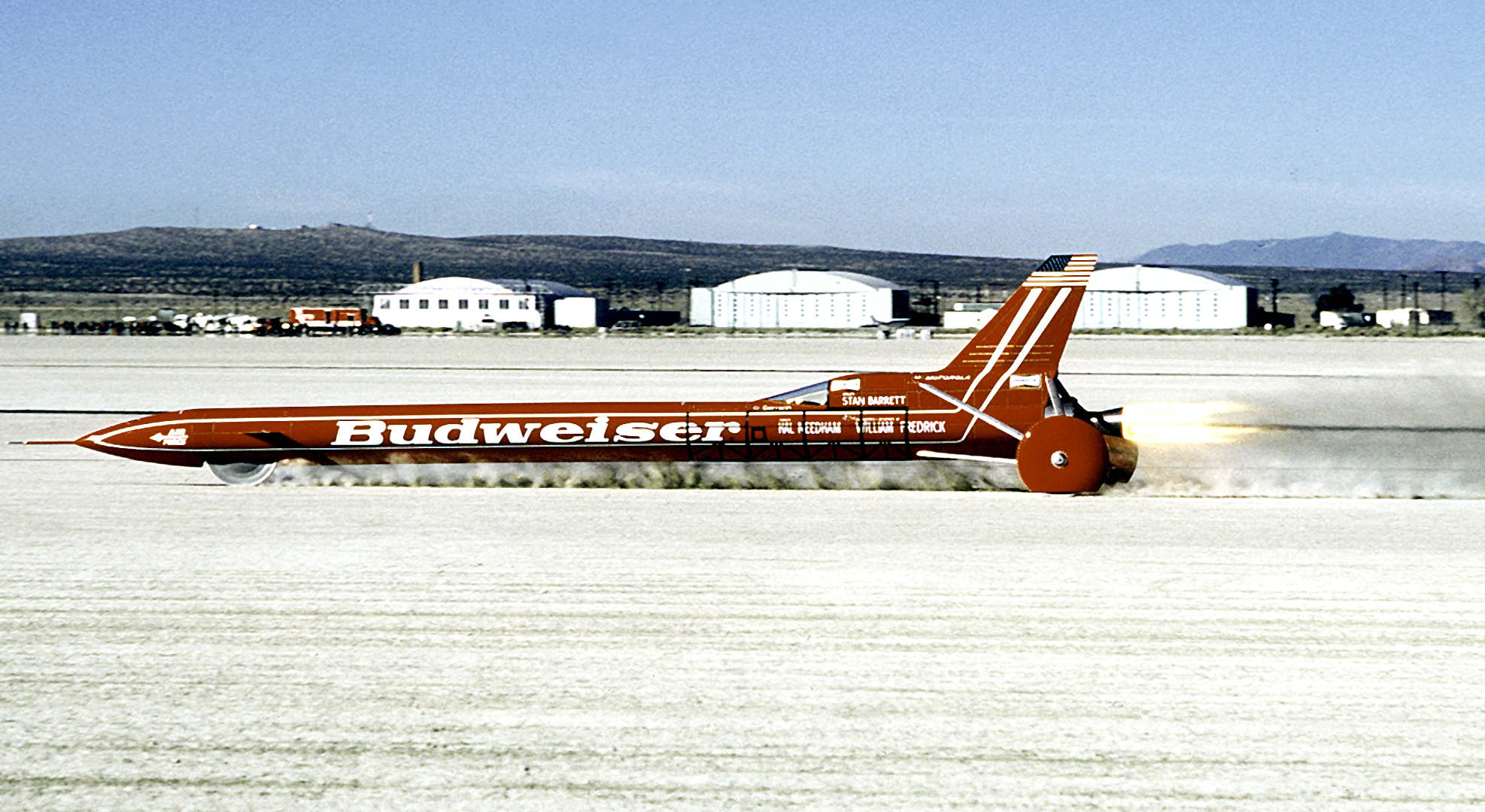
STAN BARRETT - BUDWEISER ROCKET CAR - DECEMBER 1979
The Budweiser
rocket car used a hybrid Romatec V4 rocket system, combining both liquid and solid fuel propellants and producing over 24,000 pounds of thrust or 48,000 horsepower. It worked by filtering hydrogen peroxide through a silver catalyst pack. The chemical would then decompose, producing superheated steam and oxygen well in excess of 1,370 degrees Celsius. That heat
eroded the polybutadienc solid fuel rings which automatically ignite as soon as they become gaseous.
Stan Barrett had been involved in supersonic research since the days of the X-1 rocket plane, which
he flew on the first supersonic flight on October 14, 1947. He is quoted
as saying: "There is no doubt in my mind that the rocket car exceeded the speed of sound on its run on December 17, 1979.”
Stan reached a terminal speed of 739.66mph or Mach 1.0106, even though
he ran out of fuel some 200-400 feet before the lights. We had 734mph indicated on the radar, 739mph on air speed.
He says the team had unquestionably broken the speed of sound. The
Budweiser Rocket is now in the Smithsonian Institution, the most visited museum in the world.
BLOODHOUND
SUPERSONIC CAR - GOES PART GREEN
The
Bloodhound Land Speed Record (LSR) team has confirmed plans to equip its car with a zero-emissions rocket. Powered by concentrated
hydrogen peroxide, the rocket will be used alongside a jet fighter engine to allow the car to reach speeds beyond 1,280km/h (800mph).
The Nammo rocket is a ‘monopropellant’ design that uses concentrated hydrogen peroxide (water with an extra oxygen atom – H2O2) as the oxidiser. This is pumped at high pressure through a silver gauze, which acts as a catalyst, causing it to decompose (split apart) into super-heated steam (600°C) and oxygen. The steam and oxygen are channelled through a nozzle to generate thrust. Through this process, there will be no fuel ‘combustion’ and therefore no flame nor any chemically harmful waste generated by the rocket from each run.
Work is also under way to optimise the auxiliary power unit needed to pump the rocket’s oxidiser,
by replacing the 550bhp V8 internal combustion engine
specified with an electric motor and battery pack of comparable power.
By having the battery pack and electric motor embedded, the car would be able to produce a lot of power,
in shorter bursts of around 400kW for it to be a success.
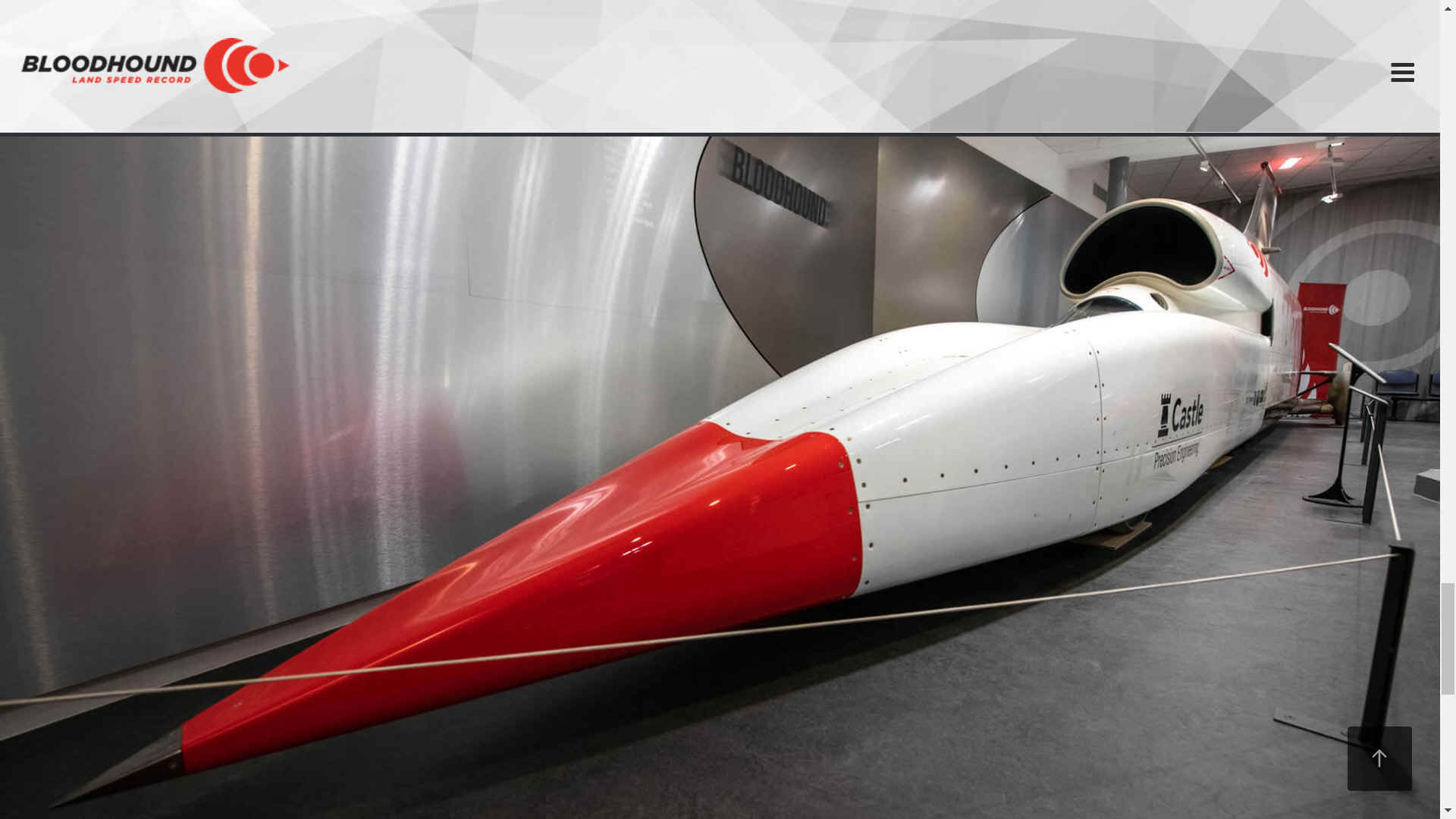
The team is also exploring the possibility of running the EJ200 jet engine on biofuel instead of Jet A fuel, further reducing the environmental impact of operating the car.
According to their website, as of August 2021, funding has been the
holdup to completing a 800mph record attempt. In January of 2021, the
BBC reported that Ian Warhurst has put the project up for sale, having
bought it himself in 2019, after the project went into administration in
October 2018, with Richard Noble, Thrust
SSC project lead, was forced to count the cost.
Whoever steps in will need pretty deep
pockets - almost $11 million (£8 million), is estimated to be needed
complete the installation of the peroxide booster, and maybe convert the
project to biofuel - having already had a coat of red and white paint as
part of their eco makeover, risk containment.
Independent analysis of the media coverage of Bloodhound LSR’s successful high-speed test programme concluded sponsors would have received a 14:1 return on their investment (ROI). Conservative estimates of the coverage for an actual land speed record attempt in 2021
were that it will be at least four times that of high-speed testing – and it is likely to be higher.
While
we applaud all manner of technological advancement, to put things in
perspective, the Elizabeth Swann could be in the water and set a zero
emission Atlantic record for similar outlay.
That said, Richard Noble has spent most of his life trying to go fast on
land, building quite a pedigree for his vehicles, likely to attract fast
car buyers quite readily. Witness the magnificent collections, such as
the National Motor Museum at Beaulieu, that must have cost more than
just a few bob to acquire. One has to marvel at the diverse designs on
wheels that brought us this far, now to electric bliss.
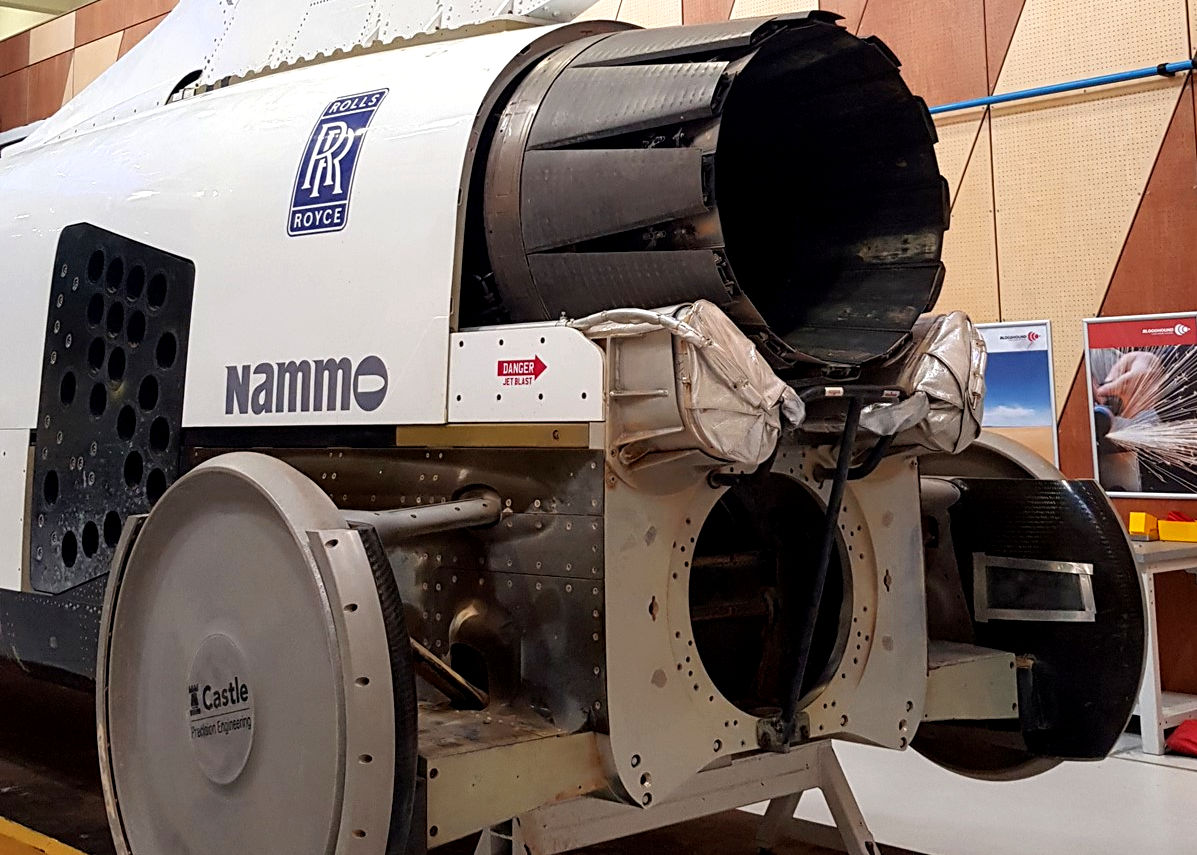
MOVING
ON - FEBRUARY
2022 - The days of jets could be numbered with more electric
aircraft taking to the skies. With more than a decade of development work under its belt, hydrogen propulsion pioneer H2Fly is now advancing efforts on a sixth-generation powertrain that it says has the potential to go into commercial service with 40-seat airliners on flights of up to around 2,500 km (1,563 miles).
In 2020, H2Fly received a permit to fly its HY4 technology demonstrator aircraft powered by a 130 kW hydrogen-electric propulsion system. The company, formed in 2014 by five engineers from the German Aerospace Center in Stuttgart and the University of
Ulm, conducted 76 flights, with some sorties lasting an hour or two.
The partners are working to be ready to start flight testing the former twin turboprop in 2025 as part of a timeline that H2Fly founder and CEO Josef Kallo told FutureFlight could lead to an aircraft being certified under EASA’s Part CS-25 rules (equivalent to FAA’s Part 25) in about seven to eight years.
DECEMBER
2021 - De Havilland Aircraft of Canada this week announced plans to power both new-build and in-service Dash 8-400 twin turboprop regional airliners with hydrogen-electric propulsion through a partnership with ZeroAvia. Under a memorandum of understanding (MoU) signed on December 14, the airframer agreed on options to buy 50 sets of ZeroAvia's in-development 2-megawatt ZA2000 powertrain, subject to finalization of partnership terms.
Following Airbus's September 2020 announcement that it is developing designs for hydrogen-powered single-aisle airliners through its ZeroE program, DeHavilland Canada is set to become the second airframer with an active program for new- build aircraft, as opposed to just retrofits for existing models. The announcement came a day after United Airlines said it would participate in a $35 million round of funding for ZeroAvia and reserve purchase rights for 100 of its powertrains to retrofit on regional jets such as the Bombardier CRJ550.
Meanwhile, ZeroAvia expects to fly a 19-seat aircraft using its ZA600 powertrain in the coming weeks in a hybrid configuration (one conventional engine, one hydrogen-electric) before flying the same aircraft using only hydrogen-electric engines next year. For its ZA2000 program, ZeroAvia aims to perform full thrust ground demonstrations of its 1.8-megawatt engine variant by the end of 2022. From there, the company plans to win certification of its ZA2000 powertrain to support 40- to 80-seat aircraft with a potential range in excess of 700 nautical miles by 2026.
By
contrast, hydrogen blue-water shipping has yet to take off.
GREEN FUEL
Hydrogen peroxide is known as a ‘green’ oxidant because it only produces
water and oxygen when it decomposes.
Although it ticks many of the boxes that are desirable in a ‘green’ fuel (its products when it is burned are only water and energy), H2 has several drawbacks that are not trivial to overcome. One of these is the storage of H2, which is largely a problem of both cost and efficiency. H2 storage has long been a problem for its utilisation as a fuel, as its energy density by volume at atmospheric pressure is far below that which would be practicable in a vehicle or even a stationary fuel storage facility.
In order for it to be viable, H2 gas must either be compressed to ,70 MPa pressure, cryogenically stored as a liquid below 21K or be physically or chemically captured in other
materials. [7] In terms of compression, storage at higher pressures allows more
fuel to be stored per unit volume, but also increases the amount of external equipment required to maintain that pressure
safely. [8,9] This raises the cost of any system incorporating pressurised H2 gas and also increases its weight.
One particularly interesting alternative fuel to H2 that has garnered some attention in the past decade is H2O2. H2O2 is well known as an oxidant and is used in several chemical and industrial processes that make use of this
property. [18–23]
It has
even been used as the oxidant in other types of fuel cells where it has been shown to perform even better than O2 in some
cases. [24–27] However, H2O2 is quite unique when applied to fuel cells because it can be both oxidised and reduced, with each
process occurring at a different electrochemical potential (NHE ¼ normal hydrogen electrode):
Anode : H2O2 ! O2 þ 2Hþ þ 2e þ 0:68 V vs NHE
Cathode : H2O2 þ 2Hþ þ 2e ! 2H2O þ 1:76 V vs NHE
Overall : 2H2O2 ! O2 þ 2H2O 1:09 V
This opens up the possibility of using H2O2 as the fuel and the oxidant in the same fuel cell with a maximum theoretical potential of 1.09 V, which is reasonably close to other fuel cells such as those using methanol/air (1.21 V) and H2/air (1.23 V).
The major advantage that an H2O2 fuel cell has over H2 is that H2O2 can be present in an aqueous solution at room temperature, thus requiring no
pressurization or additional storage media.
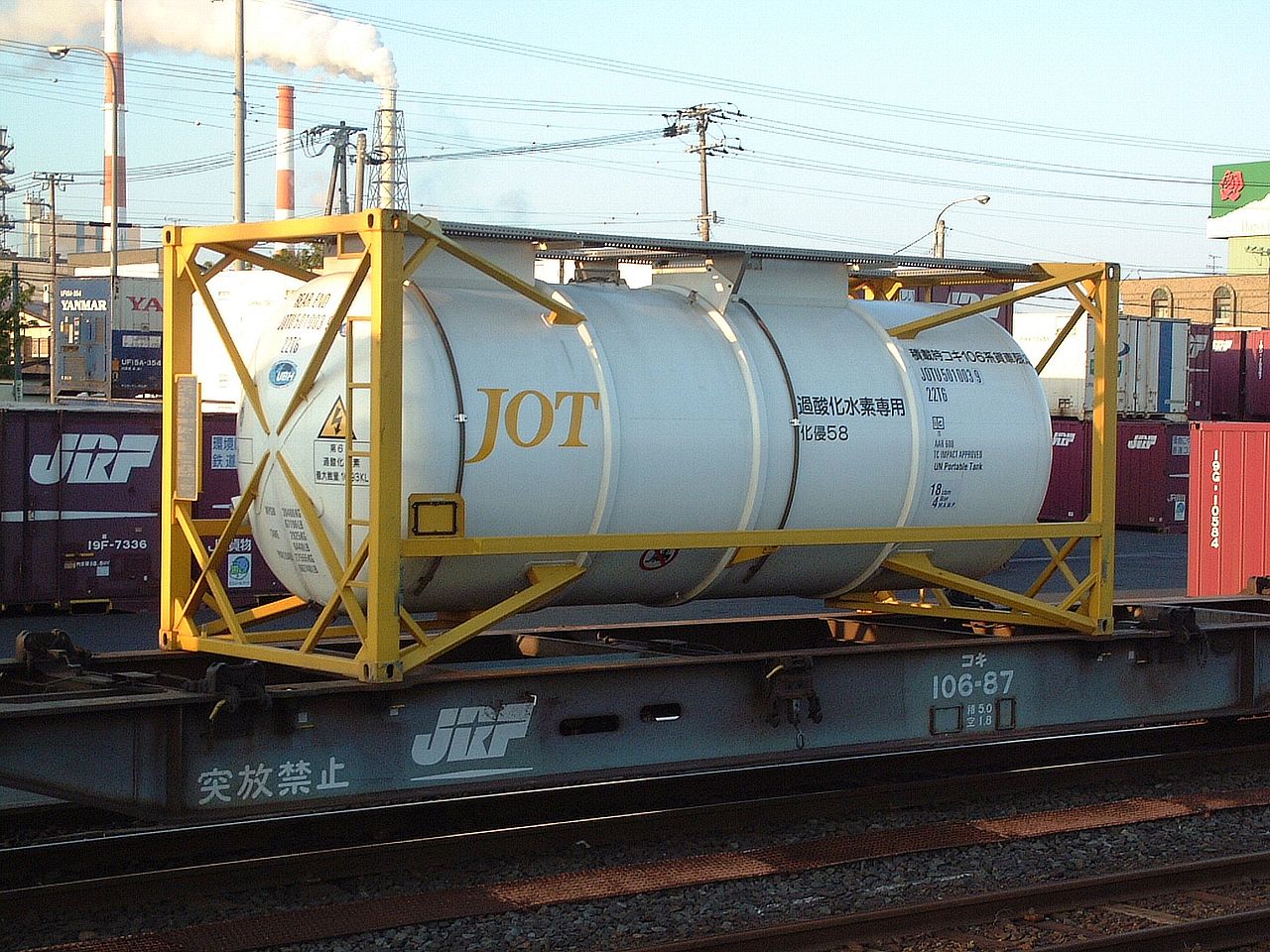
HYDROGEN PEROXIDE IN FUEL CELLS
In general, fuel cells generate power because of the difference in electrochemical potential between the oxidative and reductive reactions spontaneously occurring on the electrodes. The power generated by a fuel cell is determined by the product of the
current being drawn and the potential difference between the two electrodes at that current. As a larger current is drawn, that potential difference is reduced and as such each fuel cell will have a current at which the power is at a maximum.
Therefore,
this maximum power point is strongly influenced by the open circuit potential of the cell (which is the cell potential at which no current is being drawn from the cell) and the limiting current density (which is the total current density that can be drawn
when the electrodes are short-circuited). Although the open circuit potential (OCP) is limited by thermodynamics, increases in the limiting current density can increase the maximum achievable power density of the fuel cell as well. This requires improvement in the electrochemical catalysts that are used for both the oxidation and reduction processes. These components of an H2O2 fuel cell are particularly important when it comes to achieving OCP close to thermody-namic potential (1.09 V).
Unfortunately, this value is difficult to achieve in a real cell owing to significant overpotentials associ- ated with both reactions. This has been demonstrated by numerous studies, in particular by those who have attempted to incorporate H2O2 as an oxidant into other types of fuel cells and semi-fuel
cells. [24–26,82,83] One of the problems associated with using H2O2 as a reductant or an oxidant is that on many catalysts, it is possible for H2O2 to be reduced and oxidised on the same
surface [84–86] (Fig. 1), effectively causing the decomposition of the H2O2 and generating a ‘mixed’ potential on the electrode.
Jing et al. [87] investigated this phenomenon by measuring the OCPs of H2O2 on various noble metals in an electrochemical cell with electrolytes containing H2O2.
An ideal catalyst is therefore one that has a strong selectivity towards one of the reactions and not the other.
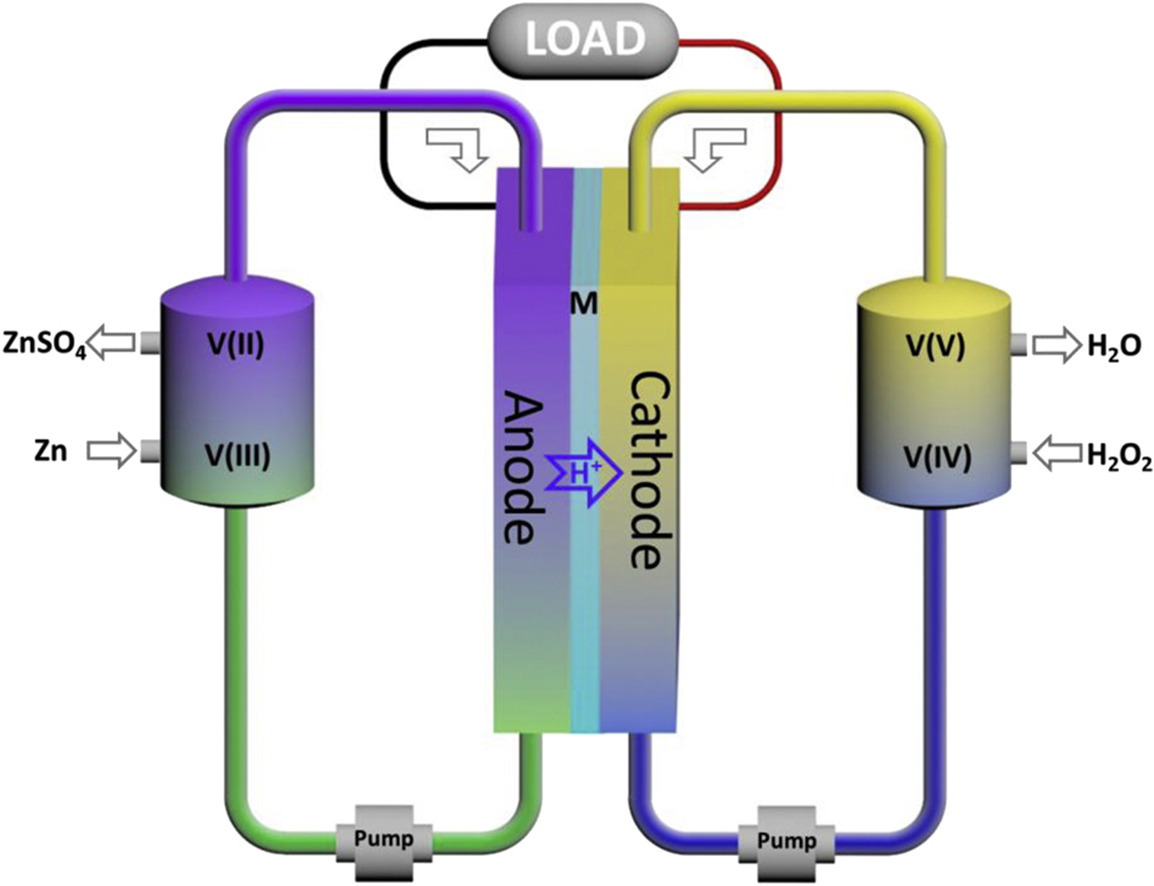
PEROXIDE
FUEL CELL CONCLUSIONS
H2O2 is a viable alternative to other ‘green’ fuels as it can be produced electrochemically from renewable feedstocks. Compared with H2 gas, it has a reasonably similar energy density per volume and can be stored without pressurisation or solid-state storage materials. Owing to its unique properties as both an oxidant and reductant, the H2O2 fuel cell is flexible in its design as either a two-compartment device with a membrane or a one-compartment device with only one electrolyte. Further work is needed to bring these types of fuel cells to practical application,
including improving the maximum power density and investigating the long-term cyclability of a complete H2O2 fuel production and utilisation system.
This can be done through investigating new catalysts that reduce the
over-potential needed for both H2O2 oxidation and reduction and also have good stability in high concentrations of H2O2. Given that H2O2 can be produced electrochemically by both O2 reduction and water
oxidation, an extremely efficient H2O2 generation system may be designed that produces both the fuel and oxidant simultaneously with no loss of energy to unneeded reactions. This, in combination with the H2O2 fuel cell, creates a reversible
fuel cell in which the
electro-generated H2O2 can be stored and transported to be utilised in a fuel cell at a later stage.
To make this practical, both the electrolyte and catalysts must be stable for long-term cyclability. There is also a need to increase the concentration of the
electro-generated H2O2 solutions either during production or by post-processing. As H2O2 is an oxidant,
in high concentrations, this fuel poses some immediate safety concerns if accidentally exposed to the environment. However, when exposed to heat and light, H2O2 quickly decomposes to water and oxygen, eliminating long-term environmental hazards. Despite these concerns, there is considerable potential in this H2O2 system as an energy storage solution and it certainly deserves further investigation and development.
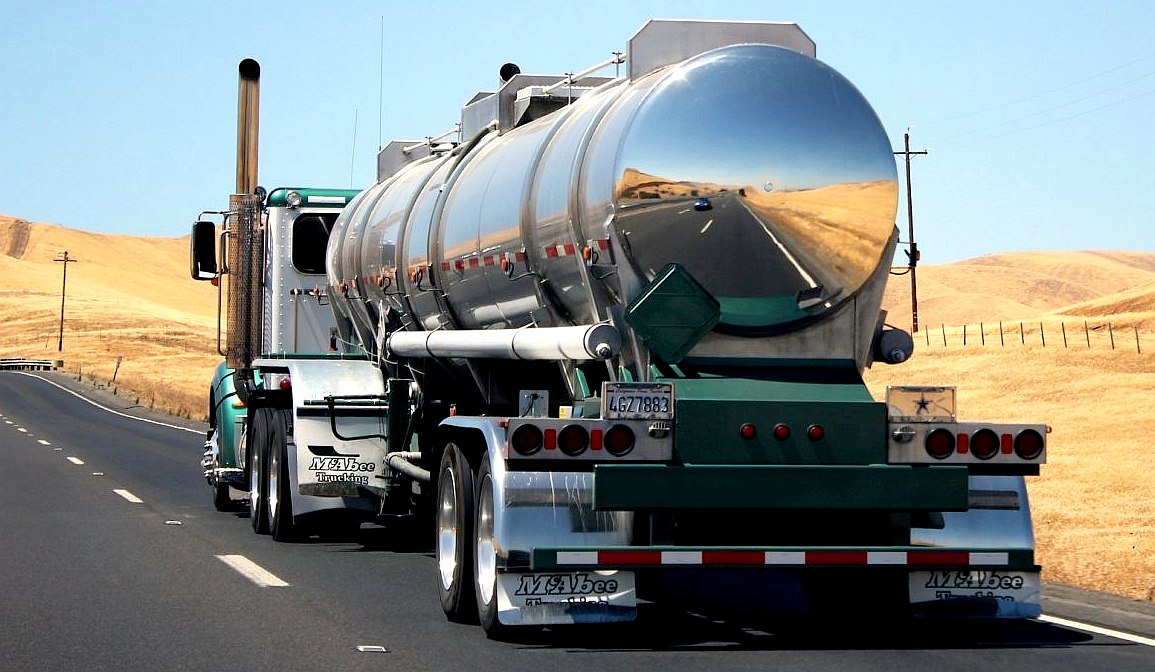
TUBE
TRAILER - Nice rig! Trucks can be used to transport hydrogen
peroxide, as can rail cars.
FILLING
THE TANKS UP
As
we write there are no marine bunkering facilities for H2O2.
A
BIT MORE ABOUT H2O2
About 60% of the world's production of hydrogen peroxide is used for
pulp and paper-bleaching. The second major industrial application is the manufacture of sodium percarbonate and sodium perborate, which are used as mild bleaches in laundry detergents. Sodium percarbonate, which is an adduct of sodium carbonate and hydrogen peroxide, is the active ingredient in such laundry products as OxiClean and Tide laundry detergent. When dissolved in water, it releases hydrogen peroxide and sodium
carbonate. These bleaching agents are only effective at wash temperatures of 60 °C (140 °F) or above and so, often are used in conjunction with bleach activators, which facilitate cleaning at lower temperatures.
Hydrogen peroxide is a chemical compound with the formula H2O2. In its pure form, it is a very pale blue liquid, slightly more viscous than water. It is used as an oxidizer, bleaching agent, and antiseptic, usually as a dilute solution (3–6% by weight) in water for consumer use, and in higher concentrations for industrial use. Concentrated hydrogen peroxide, or "high-test peroxide", decomposes explosively when heated and has been used as a propellant in rocketry.
Hydrogen peroxide is a reactive oxygen species and the simplest peroxide, a compound having an oxygen–oxygen single bond. It decomposes slowly when exposed to light, and rapidly in the presence of organic or reactive compounds. It is typically stored with a stabilizer in a weakly acidic solution in a dark bottle to block light. Hydrogen peroxide is found in biological systems including the human body. Enzymes that use or decompose
hydrogen peroxide are classified as peroxidases.
PRODUCTION
Today, hydrogen peroxide is manufactured almost exclusively by the anthraquinone process, which was originally developed by BASF in 1939. It begins with the reduction of an anthraquinone (such as 2-ethylanthraquinone or the 2-amyl derivative) to the corresponding anthrahydroquinone, typically by hydrogenation on a palladium catalyst. In the presence of oxygen, the anthrahydroquinone then undergoes autoxidation: the labile hydrogen atoms of the hydroxy groups transfer to the oxygen molecule, to give hydrogen peroxide and regenerating the anthraquinone. Most commercial processes achieve oxidation by bubbling compressed air through a solution of the anthrahydroquinone, with the hydrogen peroxide then extracted from the solution and the anthraquinone recycled back for successive cycles of hydrogenation and oxidation.
REDOX REACTIONS
The redox properties of hydrogen peroxide depend on pH as acidic conditions exacerbate the power of oxidizing agents and basic conditions the power of reducing agents. As hydrogen peroxide exhibits ambivalent redox properties, being simultaneously an oxidizer or a reductant, its redox behavior immediately depends on pH.
In acidic solutions, H2O2 is a powerful oxidizer, stronger than chlorine, chlorine dioxide, and potassium permanganate. When used for cleaning laboratory glassware, a solution of hydrogen peroxide and sulfuric acid is referred to as Piranha solution.
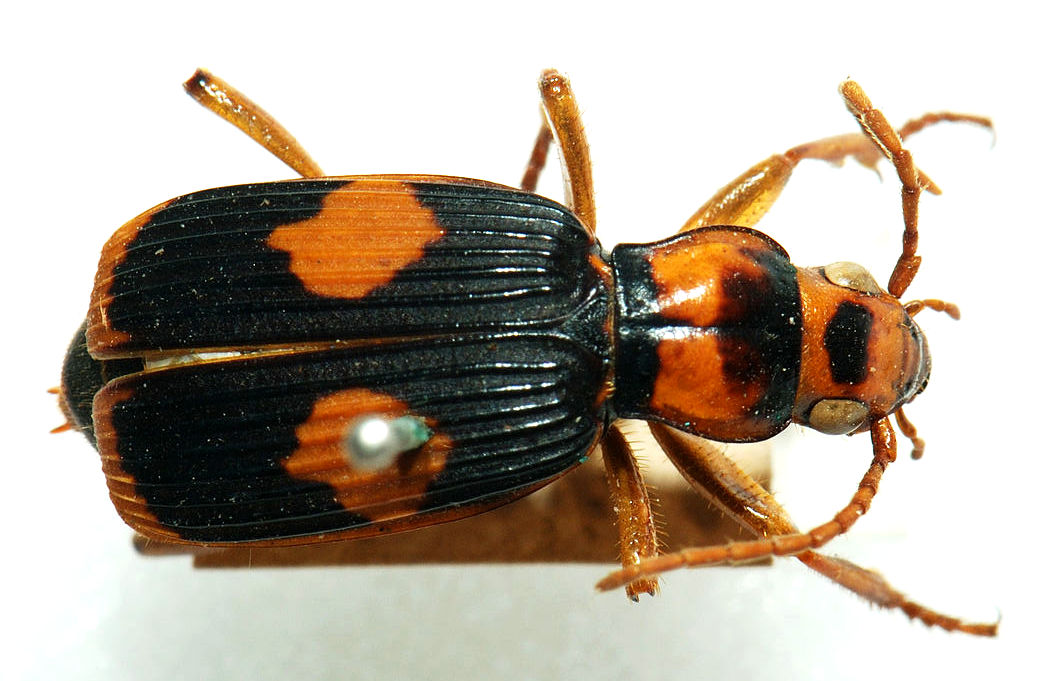
BOMBARDIER
BEETLE - Bombardier beetles
from Australia, have the infamous ability to synthesize and release rapid bursts of stinky, burning-hot liquid from their rear ends. These noxious emissions can kill other insects, or startle potential predators into backing off.
These chemical “bombs” are the source of their name: Bombardier beetles.
The beetle’s explosive power is derived primarily from the mixture of two chemical
compounds - hydroquinone and hydrogen peroxide - that are stored in separate reservoirs in the abdomen. The chemicals then pass through a valve before meeting in a special chamber, along with an enzyme that catalyzes the reaction. This creates gases that rapidly expand and give off heat.
Beetles can open and close valves to this reaction chamber rapidly, fast enough to produce up to 500 explosive bursts in a second. These insects can also aim the chemical sprays at prey, using their rear ends like a noxious water pistol.
Rumor has it that one very large specimen may attempt a land speed
record on roller skates - traveling backwards.
The African bombardier beetle (Stenaptinus insignis) can twist its abdomen to fire its spray in almost any direction in response to a threat, even targeting sites on its own back. Scientists have suggested that this incredible marksmanship may have evolved to give the beetles a fighting chance against foes like ants that can attack from any direction.
A study found that bombardier beetles have a surprisingly high survival rate when swallowed by toads, and that this appears to the be the result of their explosive defences. Scientists fed adult Asian bombardier beetles (Pheropsophus jessoensis) to two species of toad. While the toads would quickly catch and swallow the beetles, 43% vomited them out between 12-107 minutes later, suggesting that the beetles were deploying their chemical defence whilst inside the toads' stomachs.
REFERENCES
[1] S. Shafiee, E. Topal, Energy Policy 2009, 37, 181. doi:10.1016/J.
ENPOL.2008.08.016
[2] T. Zielinski, in Impact of Climate Changes on Marine Environments - (Eds J. M. W ̨esławski, K. Kulin ́ski, T. Zielinski) 2015, Ch. 1, 1–148
(Springer: Berlin).
[3] N. V. Patel, Foreign Policy 2015, 213, 28.
[4] J. Tollefson, Nature 2010, 464, 1262. doi:10.1038/4641262A
[5] B. G. Ram, K. K. Pant, in Hydrogen Fuel (Ed. B. G. Ram) 2008, Ch. 1,
- pp. 2–32 (CRC Press: Boca Raton, FL).
[6] A. Szyszka, Int. J. Hydrogen Energy 1998, 23, 849. doi:10.1016/S0360-3199(97)00172-9
[7] S. Sharma, S. K. Ghoshal, Renew. Sustain. Energy Rev. 2015, 43,1151. doi:10.1016/J.RSER.2014.11.093
[8] R. Ortiz Cebolla, B. Acosta, P. Moretto, N. Frischauf, F. Harskamp, C. Bonato, D. Baraldi, Int. J. Hydrogen Energy 2014, 39, 6261.
doi:10.1016/J.IJHYDENE.2013.10.038
[9] M. Royle, D. Willoughby, Process Saf. Environ. Prot. 2011, 89, 452. doi:10.1016/J.PSEP.2011.09.003
[10] L. Ma, D. J. Mihalcik, W. Lin, J. Am. Chem. Soc. 2009, 131, 4610. doi:10.1021/JA809590N
[11] I. A. Ibarra, S. Yang, X. Lin, A. J. Blake, P. J. Rizkallah, H. Nowell,
D. R. Allan, N. R. Champness, P. Hubberstey, M. Schroder, Chem. Commun. 2011, 8304. doi:10.1039/C1CC11168J
[12] Y. Yan, S. Yang, A. J. Blake, M. Schro ̈der, Acc. Chem. Res. 2014, 47,
296. doi:10.1021/AR400049H
[13] M. Lototskyy, V. A. Yartys, J. Alloys Compd. 2015, 645, S365. doi:10.1016/J.JALLCOM.2014.12.107
[14] F. Schuth, B. Bogdanovic, M. Felderhoff, Chem. Commun. 2004, 2249. doi:10.1039/B406522K
[15] C. M. Rangel, V. R. Fernandes, Y. Slavkov, L. Bozukov, Int. J. Hydrogen Energy 2009, 34, 4587. doi:10.1016/J.IJHYDENE.2008.
10.082
[16] I. P. Jain, Int. J. Hydrogen Energy 2009, 34, 7368. doi:10.1016/J.IJHYDENE.2009.05.093
[17] S. Niaz, T. Manzoor, A. H. Pandith, Renew. Sustain. Energy Rev. 2015, 50, 457. doi:10.1016/J.RSER.2015.05.011
[18] U. Suess Hans, Pulp Bleaching Today 2010 (De Gruyter: Berlin).
[19] K. Sato, R. Noyori, Science 1998, 281, 1646. doi:10.1126/SCIENCE. 281.5383.1646
[20] A. Aleboyeh, H. Aleboyeh, Y. Moussa, Dyes Pigments 2003, 57, 67. doi:10.1016/S0143-7208(03)00010-X
[21] P. Blach, Z. Bo ̈strom, S. Franceschi-Messant, A. Lattes, E. Perez,
I. Rico-Lattes, Tetrahedron 2010, 66, 7124. doi:10.1016/J.TET.2010. 06.093786 C. J. McDonnell-Worth and D. R. MacFarlane
[22] H. Egami, T. Oguma, T. Katsuki, J. Am. Chem. Soc. 2010, 132, 5886. doi:10.1021/JA100795K
[23] L. Cui, S. Furuhashi, Y. Tachikawa, N. Tada, T. Miura, A. Itoh, Tetrahedron Lett. 2013, 54, 162. doi:10.1016/J.TETLET.2012.
10.119
[24] N. A. Choudhury, R. K. Raman, S. Sampath, A. K. Shukla, J. Power Sources 2005, 143, 1. doi:10.1016/J.JPOWSOUR.2004.08.059
[25] S. J. Lao, H. Y. Qin, L. Q. Ye, B. H. Liu, Z. P. Li, J. Power Sources
2010, 195, 4135. doi:10.1016/J.JPOWSOUR.2010.01.059
[26] G. Agladze, P. Nikoleishvili, V. Kveselava, G. Tsurtsumia, G. Gorelishvili, D. Gogoli, I. Kakhniashvili, J. Power Sources 2012,
218, 46. doi:10.1016/J.JPOWSOUR.2012.06.086
[27] D. M. F. Santos, P. G. Saturnino, R. F. M. Lobo, C. A. C. Sequeira,
J. Power Sources 2012, 208, 131. doi:10.1016/J.JPOWSOUR.2012. 02.016
[28] R. S. Disselkamp, Int. J. Hydrogen Energy 2010, 35, 1049. doi:10. 1016/J.IJHYDENE.2009.11.073
[29] S. Haji, B. Benstaali, N. Al-Bastaki, Chem. Eng. J. 2011, 168, 134.
doi:10.1016/J.CEJ.2010.12.050
[30] V. M. Daskalaki, E. S. Timotheatou, A. Katsaounis, D. Kalderis, Desalination 2011, 274, 200. doi:10.1016/J.DESAL.2011.02.009
[31] S. Yang, P. Wang, X. Yang, L. Shan, W. Zhang, X. Shao, R. Niu, J. Hazard. Mater. 2010, 179, 552. doi:10.1016/J.JHAZMAT.2010.03.
039
[32] D. Sloboda-Rozner, P. L. Alsters, R. Neumann, J. Am. Chem. Soc. 2003, 125, 5280. doi:10.1021/JA0344821
[33] K.-P. Ho, K.-Y. Wong, T. H. Chan, Tetrahedron 2006, 62, 6650. doi:10.1016/J.TET.2005.12.075
[34] Y. Xu, N. R. B. J. Khaw, Z. Li, Green Chem. 2009, 11, 2047. doi:10.
1039/B913077B
[35] P. Jin, Z. Zhao, Z. Dai, D. Wei, M. Tang, X. Wang, Catal. Today 2011, 175, 619. doi:10.1016/J.CATTOD.2011.04.041
[36] J. Kim, S. Jung, S. Park, S. Park, Tetrahedron Lett. 2011, 52, 2866.
doi:10.1016/J.TETLET.2011.03.115
[37] F. Nikbakht, A. Heydari, Tetrahedron Lett. 2014, 55, 2513. doi:10. 1016/J.TETLET.2014.03.017
[38] Q. Chen, J. Clean. Prod. 2006, 14, 708. doi:10.1016/J.JCLEPRO. 2005.03.025
[39] M. Giomo, A. Buso, P. Fier, G. Sandona‘, B. Boye, G. Farnia, Elec-trochim. Acta 2008, 54, 808. doi:10.1016/J.ELECTACTA.2008.06.038
[40] G. Fioroni, F. Fringuelli, F. Pizzo, L. Vaccaro, Green Chem. 2003, 5,
425. doi:10.1039/B303883A
[41] G. B. Payne, J. Am. Chem. Soc. 1959, 81, 4901. doi:10.1021/JA01527A035
[42] I. Oller, S. Malato, J. A. Sa ́nchez-Pe ́rez, Sci. Total Environ. 2011,
409, 4141. doi:10.1016/J.SCITOTENV.2010.08.061
[43] I. Yamanaka, T. Onisawa, T. Hashimoto, T. Murayama, Chem-SusChem 2011, 4, 494. doi:10.1002/CSSC.201000263
[44] M. A. Ghanem, A. M. Al-Mayouf, M. N. Shaddad, F. Marken, Electrochim. Acta 2015, 174, 557. doi:10.1016/J.ELECTACTA.
2015.06.017
[45] A. von Weber, E. T. Baxter, H. S. White, S. L. Anderson, J. Phys. Chem. C 2015, 119, 11160. doi:10.1021/JP5119234
[46] M. Gara, E. Laborda, P. Holdway, A. Crossley, C. J. V. Jones, R. G.
Compton, Phys. Chem. Chem. Phys. 2013, 15, 19487. doi:10.1039/C3CP53684J
[47] A. Ohma, K. Fushinobu, K. Okazaki, Electrochim. Acta 2010, 55, 8829. doi:10.1016/J.ELECTACTA.2010.08.005
[48] M. Gennari, D. Brazzolotto, J. Pe ́caut, M. V. Cherrier, C. J. Pollock,
S. DeBeer, M. Retegan, D. A. Pantazis, F. Neese, M. Rouzie‘res, R. Cle ́rac, C. Duboc, J. Am. Chem. Soc. 2015, 137, 8644. doi:10.1021/JACS.5B04917
[49] L. R. Aveiro, A. G. M. da Silva, V. S. Antonin, E. G. Candido, L. S.
Parreira, R. S. Geonmonond, I. C. de Freitas, M. R. V. Lanza, P. H. C. Camargo, M. C. Santos, Electrochim. Acta 2018, 268, 101. doi:10.
1016/J.ELECTACTA.2018.02.077
[50] W. R. P. Barros, Q. Wei, G. Zhang, S. Sun, M. R. V. Lanza, A. C. Tavares, Electrochim. Acta 2015, 162, 263. doi:10.1016/J.ELEC
TACTA.2015.02.175
[51] J. S. Jirkovsky ́, I. Panas, E. Ahlberg, M. Halasa, S. Romani, D. J.
Schiffrin, J. Am. Chem. Soc. 2011, 133, 19432. doi:10.1021/ JA206477Z
[52] S. Siahrostami, A. Verdaguer-Casadevall, M. Karamad, D. Deiana, P. Malacrida, B. Wickman, M. Escudero-Escribano, E. A. Paoli, R.
Frydendal, T. W. Hansen, I. Chorkendorff, I. E. L. Stephens, J. Rossmeisl, Nat. Mater. 2013, 12, 1137. doi:10.1038/NMAT3795
[53] S. Kakuda, R. L. Peterson, K. Ohkubo, K. D. Karlin, S. Fukuzumi, J. Am. Chem. Soc. 2013, 135, 6513. doi:10.1021/JA3125977
[54] M. Campos, W. Siriwatcharapiboon, R. J. Potter, S. L. Horswell, Catal. Today 2013, 202, 135. doi:10.1016/J.CATTOD.2012.05.015
[55] I. Yamanaka, R. Ichihashi, T. Iwasaki, N. Nishimura, T. Murayama, W. Ueda, S. Takenaka, Electrochim. Acta 2013, 108, 321. doi:10.
1016/J.ELECTACTA.2013.06.072
[56] K. Mase, K. Ohkubo, S. Fukuzumi, J. Am. Chem. Soc. 2013, 135, 2800. doi:10.1021/JA312199H
[57] G. Go ̈ransson, E. Ahlberg, Electrochim. Acta 2014, 146, 638. doi:10.
1016/J.ELECTACTA.2014.08.127
[58] S. Chen, Z. Chen, S. Siahrostami, D. Higgins, D. Nordlund, D. Sokaras, T. R. Kim, Y. Liu, X. Yan, E. Nilsson, R. Sinclair, J. K.
Nłrskov, T. F. Jaramillo, Z. Bao, J. Am. Chem. Soc. 2018, 140, 7851. doi:10.1021/JACS.8B02798
[59] Y. Sun, I. Sinev, W. Ju, A. Bergmann, S. Dresp, S. Ku ̈hl, C. Spo ̈ri,
H. Schmies, H. Wang, D. Bernsmeier, B. Paul, R. Schmack, R. Kraehnert, B. Roldan Cuenya, P. Strasser, ACS Catal. 2018, 8,
2844. doi:10.1021/ACSCATAL.7B03464
[60] S. Kabir, K. Artyushkova, A. Serov, P. Atanassov, ACS Appl. Mater. Interfaces 2018, 10, 11623. doi:10.1021/ACSAMI.7B18651
[61] C. Di Bari, S. Shleev, A. L. De Lacey, M. Pita, Bioelectrochemistry
2016, 107, 30. doi:10.1016/J.BIOELECHEM.2015.10.003
[62] A. Bonakdarpour, M. Lefevre, R. Yang, F. Jaouen, T. Dahn, J.-P. Dodelet, J. R. Dahn, Electrochem. Solid-State Lett. 2008, 11, B105.
doi:10.1149/1.2904768
[63] V. G. Khomenko, K. V. Lykhnytskyi, V. Z. Barsukov, Electrochim. Acta 2013, 104, 391. doi:10.1016/J.ELECTACTA.2013.04.019
[64] T.-P. Fellinger, F. Hasche ́, P. Strasser, M. Antonietti, J. Am. Chem.
Soc. 2012, 134, 4072. doi:10.1021/JA300038P
[65] T. Murayama, I. Yamanaka, J. Phys. Chem. C 2011, 115, 5792. doi:10.1021/JP1109702
[66] I. Yamanaka, T. Murayama, Angew. Chem. Int. Ed. 2008, 47, 1900. doi:10.1002/ANIE.200704431
[67] V. Cˇ olic ́, S. Yang, Z. Re ́vay, I. E. L. Stephens, I. Chorkendorff,
Electrochim. Acta 2018, 272, 192. doi:10.1016/J.ELECTACTA. 2018.03.170
[68] F. Yu, Y. Chen, H. Ma, New J. Chem. 2018, 42, 4485. doi:10.1039/C7NJ04925K
[69] V. L. Kornienko, G. A. Kolyagin, G. V. Kornienko, V. A. Parfenov, I.
V. Ponomarenko, Russ. J. Electrochem. 2018, 54, 258. doi:10.1134/S1023193518030060
[70] Y. Liu, X. Quan, X. Fan, H. Wang, S. Chen, Angew. Chem. Int. Ed. 2015, 54, 6837. doi:10.1002/ANIE.201502396
[71] B. B. Blizanac, P. N. Ross, N. M. Markovic, Electrochim. Acta 2007,
52, 2264. doi:10.1016/J.ELECTACTA.2006.06.047
[72] J. F. Pe ́rez, A. Galia, M. A. Rodrigo, J. Llanos, S. Sabatino, C. Sa ́ez,
B. Schiavo, O. Scialdone, Electrochim. Acta 2017, 248, 169. doi:10. 1016/J.ELECTACTA.2017.07.116
[73] Y. Shiraishi, S. Kanazawa, Y. Kofuji, H. Sakamoto, S. Ichikawa, S. Tanaka, T. Hirai, Angew. Chem. Int. Ed. 2014, 53, 13454. doi:10.
1002/ANIE.201407938
[74] C. Kormann, D. W. Bahnemann, M. R. Hoffmann, Environ. Sci. Technol. 1988, 22, 798. doi:10.1021/ES00172A009
[75] N. Her, J.-S. Park, Y. Yoon, Chem. Eng. J. 2011, 166, 184. doi:10. 1016/J.CEJ.2010.10.059
[76] K. Mase, M. Yoneda, Y. Yamada, S. Fukuzumi, ACS Energy Lett. 2016, 1, 913. doi:10.1021/ACSENERGYLETT.6B00415
[77] Y. Isaka, K. Oyama, Y. Yamada, T. Suenobu, S. Fukuzumi, Catal. Sci. Technol. 2016, 6, 681. doi:10.1039/C5CY01845E
[78] A. Izgorodin, E. Izgorodin, D. R. MacFarlane, Energy Environ. Sci. 2012, 5, 9496. doi:10.1039/C2EE21832A
Towards Direct Hydrogen Peroxide Fuel Cells 787
|